注塑件成型的工艺条件
注塑件成型是一门工程技术,它所涉及的内容是将塑料转变为有用并能保持原有性能的制品。注射成型的重要工艺条件是影响塑化流动和冷却的温度,压力和相应的各个作用时间?! ∥露瓤刂啤 ?、料筒温度:注射模塑过程需要控制的温度有料筒温度,喷嘴温度和模具温度等。前两种温度主要影响塑料的塑化和流动,而后一种温度主要是影响塑料的流动和冷却。每一种塑料都具有不同的流动温度,同一种塑料,由于来源或牌号不同,其流动温度及分解温度是有差别的,这是由于平 均分子量和分子量分布不同所致,塑料在不同类型的注射机内的塑化过程也是不同的,因而选择料筒温度也不相同。 2、喷嘴温度:喷嘴温度通常是略低于料筒最高温度的,这是为了防止熔料在直通式喷嘴可能发生的"流涎现象"。喷嘴温度也不能过低,否则将会造成熔料的早凝而将喷嘴堵*,或者由于早凝料注入模腔而影响制品的性能 3、模具温度:模具温度对制品的内在性能和表观质量影响很大。模具温度的高低决定于塑料结晶性的有无、制品的尺寸与结构、性能要求,以及其它工艺条件(熔料温度、注射速度及注射压力、模塑周期等)?! ⊙沽刂疲?注塑件过程中压力包括塑化压力和注射压力两种,并直接影响塑料的塑化和制品质量。 1、塑化压力:(背压)采用螺杆式注射机时,螺杆顶部熔料在螺杆转动后退时所受到的压力称为塑化压力,亦称背压。这种压力的大小是可以通过液压系统中的溢流阀来调整的。在注射中,塑化压力的大小是随螺杆的转速都不变,则增加塑化压力时即会提高熔体的温度,但会减小塑化的速度。此外,增加塑化压力常能使熔体的温度均匀,色料的混合均匀和排出熔体中的气体。一般操作中,塑化压力的决定应在保证制品质量优良的前提下越低越好,其具体数值是随所用的塑料的品种而异的,但通常很少超过20公斤/平方厘米?! ?、注射压力:在当前生产中,几乎所有的注射机的注射压力都是以柱塞或螺杆顶部对塑料所施的压力(由油路压力换算来的)为准的。注射压力在注塑件成型中所起的作用是,克服塑料从料筒流向型腔的流动阻力,给予熔料充模的速率以及对熔料进行压实?! 〕尚椭芷凇 ⊥瓿梢淮巫⑸淠K芄趟璧氖奔涑瞥尚椭芷冢渤颇K苤芷?。它实际包括以下几部分: 成型周期:成型周期直接影响劳动生产率和设备利用率。因此,在生产过程中,应在保证质量的前提下,尽量缩短成型周期中各个有关时间。在整个成型周期中,以注射时间和冷却时间最重要,它们对制品的质量均有决定性的影响。注射时间中的充模时间直接反比于充模速率,生产中充模时间一般约为3-5秒?! ∽⑸涫奔渲械谋Q故奔渚褪嵌孕颓荒谒芰系难沽κ奔?在整个注射时间内所占的比例较大,一般约为20-120秒(特厚制件可高达5~10分钟)。在浇口处熔料封冻之前,保压时间的多少,对制品尺寸准确性有影响,若在以后,则无影响。保压时间也有最惠值,已知它依赖于料温,模温以及主流道和浇口的大小。如果主流道和浇口的尺寸以及工艺条件都是正常的,通常即以得出制品收缩率波动范围最小的压力值为准。冷却时间主要决定于制品的厚度,塑料的热性能和结晶性能,以及模具温等。冷却时间的终点,应以保证制品脱模时不引起变动为原则,冷却时间性一般约在30~120秒钟之间,冷却时间过长没有必要,不仅降低生产效率,对复杂制件还将造成脱模困难,强行脱模时甚至会产生脱模应力。成型周期中的其它时间则与生产过程是否连续化和自动化以及连续化和自动化的程度等有关。 一般的注塑件机可以根据以下的程序作调校: 根据原料供应商的资料所提供的温度范围,将料筒温度调至该范围的中间,并调整模温?! 」兰扑璧纳浣毫浚⑺芗髦凉兰频淖畲笊浣毫康娜种?。调校倒索(抽胶)行程。估计及调校二级注塑件时间,将二级注塑件压力调至零。 初步调校一级注塑件压力至注塑件机极限的一半(50%) ;将注塑件速度调至最高。 估计及调校所需要的冷却时间。 将背压调至3.5bar。 清除料筒内已降解了的树脂。 采用半自动注塑件模式;开始注塑件程序,观察螺杆的动作?! 【托枰实钡鹘谏浣核俣群脱沽?,若要使充模时间缩短,可以增加注塑件压力。如前所述,由于十足充模之前会有一个过程,充模最终压力可以调至一级注塑件压力的100%。压力最终都要调得够高,使可以达到的最大速度不受设定压力限制。若有溢料,可以把速度减低?! ∶抗鄄煲桓鲋芷谥螅惆焉浣毫考白坏愕鹘?。设定程序,使可以在第一级注塑件时已能获得按射胶重量计算达到95-98% 的充模?! 〉钡谝患蹲⑺芗淖⑸淞?、转换点、注塑件速度及压力均调节妥当后,便可进行第二级的保压压力的调校程序?! “葱枰实钡餍1Q寡沽?,但切勿过份充填模腔?! 〉餍B莞怂俣?,确保刚在周期完成之前熔胶已完成,而注塑件周期又没有受到限制?! ∷醵讨芷谑奔溆杼岣呱省 《源蟛糠值淖⑺芗汤此?,注塑件周期可直接影响以下两个主要目的:1、每天从机械中得到更多的制件;2、制件合乎客人的要求?! ∽⑺芗芷谟梢韵伦槌桑骸 ≈芷诳?-螺杆开始前进,注射; 制件浇口冷却 螺杆开始转动--塑化行程开始 螺杆回位完成--螺杆转动停止 如必要的话抽胶发生 模具打开(可能包括模芯的拉出) 制件充分冷却便可以顶出 顶出 模具闭合(可能包括模芯的回位) 模具闭上--周期重新开始?! ∽远⑺芗芷谑窃诔中南嗤涡蛳?,同样的事情一次又一次地重复。周期有三个主要部分: 开模时间 ;填充时间;模具闭合时间; 保压时间 提高生产力的目标是在极短时间内完成所有必要的动作,完成顶出,并确保模具得到?;ぃòɡ龊屯嘶鼗楹筒辔荒P荆?。所以,任何,延迟开模时间的模具或注塑件机的问题必须维修。另外,如每次注射的开模时间都不一样,制件将亦不一样。 注塑件填充模腔(由1-2) 以流动性较好的材料而言,这填充时间应占整个周期1/10至1/8的时间,填充时最关键的是快速及稳定的螺杆推进时间,及最低和稳定的注塑件压力?! 〉甭莞讼蚯巴平芴逵闪瞎芫缇?,竖流道,横流通,浇口,再射入模腔,当中会遇到阻力。这阻力是由喷咀直径、流道尺寸、浇口大小、产品厚度,以及模具排气设计所影响。 流动阻力应在模具内改善及减少,以达至填充平衡及稳定。否则由于填充不均匀而导致不同模腔所注塑件的制品尺寸不同,强度不足,或外观不良?! ”Q故奔洌?-3) 当注塑件结晶形材料时,保压时间是最重要的一段过程。这段时间是由熔体填充模腔99%开始至浇口凝固为终止。模件的强度及韧性都是决定于注塑件后有否保持压力到熔体上直至部件/浇口凝固。保持压力时亦要预先保留一小段的熔胶位置在螺杆前。这保压的一段就是防止熔体凝固收缩后的空洞,或浇口位置的弱处等导致模件强度不足的关键?! ±淙词奔洌?-7) 当熔体进入模腔,碰到金属表面时,熔体冷却的步骤就己经开始。由于聚甲醛,尼龙,及聚碳等半结晶材料的凝固温度很高,所以需要冷却的时间便很少。若以一般模件来说,在熔胶完成后,模件应该已经有足够的冷却时间。如果在顶出模件时发现出问题的话,可慢慢将冷却时间延长,直至问题解决为止?! 】J奔洌?-11) 模具开放的时间是整个周期的重要部份,特别是对有装嵌件的模具更是如此,甚至在比较标准的模具中,模具开放时间也经常高过整个周期的20%?! ∮跋炜5囊蛩兀骸 〉谝幌钜悸堑氖悄>叩乃俣群鸵贫嗬耄>咴诖蚩⒍コ鲋萍讨幸贫木嗬胗跎僖悦饫朔岩贫奔?,当然,模具移动必须在模具再次关闭前足以让制件顺利脱离模具,所以,让制件脱模所需移动距离愈短,则其所花的的间愈少,当注射成型机处于良好状态,从高速打开到低速顶出的转换能够相当平稳。设备需要一些保养以完成这些速度上的变化,但是这些花费可以从模塑时间减少,节省时间而得到多倍的回报。为了达到最少的模具移动时间,调整减速限制开关,以便预出过程中模具不会过于接触或破坏制件,并优化行程的高速段。再者,适当的周期性的保养以确保这减速每次能重复。产生锁模压力时间在整个模具开放时间中是另一个阻延,这个时间可能经过机械磨损和液压阀失效的影响,因此周期性的机械保养可以保持良好的操作状态?! ∽⒁猓骸 ∷醵棠>叽蚩谐痰剿匦璧淖钚?,以便制件和流道脱落 排除任何使顶出困难的因素,像顶针周围的飞边(披锋) 缩短顶出行程到所必需的最小值 用最快的开模和闭模速度,同时要适当慢慢地中止和闭合以防止损坏模具 寻找所有闭模和产生锁模压力中的阻延,它们表示机械或液压阀的故障 在模具中大量的装嵌件活动也增长模具开放时间。稍加考虑产品设计(减少倒扣)就往往能使顶出动作自动化或半自动化进行 若这延误是由模具损耗所导致,理应修理模具,以减低延误?! ⊙闪己玫淖⑺芗僮飨肮摺 ⊙闪己玫淖⑺芗僮飨肮叨蕴岣呋魇倜蜕踩即笥泻么Α! 】埃骸 。?)检查电器控制箱内是否有水、油进入,若电器受潮,切勿开机。应由维修人员将电器零件吹干后再开机?! 。?)检查供电电压是否符合,一般不应超过15%。 ?。?)检查急???,前后安全门开关是否正常。验证电动机与油泵的转动方向是否一致?! 。?)检查各冷却管道是否畅通,并对油冷却器和机筒端部的冷却水套通入冷却水?! 。?)检查各活动部位是否有润滑油(脂),并加足润滑油?! 。?)打开电热,对机筒各段进行加温。当各段温度达到要求时,再保温一段时间,以使机器温度趋于稳定。保温时间根据不同设备和塑料原料的要求而有所不同?! 。?)在料斗内加足足够的塑料。根据注塑件不同塑料的要求,有些原料最好先经过干燥。 ?。?)要盖好机筒上的隔热罩,这样可以节省电能,又可以延长电热圈和电流接触器的寿命?! 〔僮鞴讨校骸 。?)不要为贪图方便,随意取消安全门的作用?! 。?)注意观察压力油的温度,油温不要超出规定的范围。液压油的理想工作温度应保持在45~50℃之间,一般在35~60℃范围内比较合适?! 。?)注意调整各行程限位开关,避免机器在动作时产生撞击?! 」ぷ鹘崾保骸 。?)?;?,应将机筒内的塑料清理干净,预防剩料氧化或长期受热分解?! 。?)应将模具打开,使肘杆机构长时间处于闭锁状态?! 。?)车间必须备有起吊设备。装拆模具等笨重部件时应十分小心,以确保生产安全?! ∽⑺芗褂弥械囊恍┲丁 ”逞沟墓τ谩 ”逞沟挠τ每梢匀繁B莞嗽谛次皇保懿愎坏幕的芰?,把塑料熔化及混合。背压还有以下的用途: 把挥发性气体,包括空气排出射料缸外; 把附加剂(例如色粉、色种、防静电剂、滑石粉等) 和熔料均匀地混合起来; 使流经螺杆长度的熔料均匀化; 提供均匀稳定的塑化材料以获得精确的成品重量控制?! ∷∮玫谋逞故涤κ蔷】赡艿氐停ɡ?-15bar,或58-217.5psi),只要熔料有适当的密度和均匀性,熔料内并没有气泡、挥发性气体和未完全塑化的塑料便可以。 背压的利用使注塑件机的压力温度和熔料温度上升。上升的幅度和所设定背压数值有关。较大型的注塑件机(螺杆直径超过70mm/2.75in)的油路背压可以高至25-40bar(362.5-580psi)。但需要注意,太高的背压引起在射料筒内的熔料温度过高,这情况对于热量很敏感的塑料生产是有破坏作用的?! 《姨叩谋逞挂嘁鹇莞斯蠛筒还嬖虻脑轿磺榭?,使射胶量极不稳定。越位的多少是受着塑料的黏弹性特性所影响。熔料所储藏的能量愈多,螺杆在停止旋转时,产生突然的向后跳动,一些热塑性塑料的跳动现象较其他的塑料厉害,例如LDPE、HDPE、PP、EVA、PP/EPDM合成物和PPVC,比较起GPPS、HIPS、POM、PC、PPO-M和PMMA都较易发生跳动现象?! ∥嘶竦米罴训纳跫返谋逞股瓒ㄖ廖匾?,这样,熔料可以得到适当的混合,而螺杆的越位范围亦不会超过0.4mm(0.016in)?! ∧>叩目稀 ∫话憷此?,大多数注塑件机所用的模具开合时间比引用的时间要慢(约100-359%),这个差别与模具的重量、大小和复杂性有关,也和模具的安全?;ぃㄔ诳系牟僮髦蟹乐鼓>呤芩穑┯泄??! 〉湫偷哪>呖鲜奔淙缦拢╰cm:注塑件机引用的时间单位): 传统的双板模具:1-2tcm 复合模具(包括侧模芯和旋出装置的使用)和多板模具:2-3.5tcm 如模具开合的时间比实际运作的时间多15%,那么便需要修改模具或使用另一台注塑件机来缩短时间。较新型注塑件机能提供更快的开合速度,使用低模具开合(模具传感)压力,以启动锁模力合紧模具。 注塑件机操作员经常没有注意某一特定注塑件机的机板速度或时间,而以个人经验来设定模具开合时间,这样往往会令运作时间长。在一个十秒的运作上减少一秒,便立即获得10%的改善,这个改善往往就是构成盈利和亏损的差别。
17898826917
邮 箱:40045692@qq.com
Q Q:40045692
地 址:上海市奉贤区南桥镇国顺路936号5幢
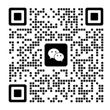
Copyright ? 2018-2022 上海道勤塑化有限公司 版权所有 备案号:沪ICP备19016906号
17898826917
邮 箱:40045692@qq.com
Q Q:40045692
地 址:上海市奉贤区南桥镇国顺路936号5幢
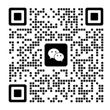
Copyright ? 2018 上海道勤塑化有限公司 版权所有
备案号:沪ICP备19016906号